Underhåll för blandade fordonsparker: Att ta det säkra för det osäkra kan bli en dyr strategi
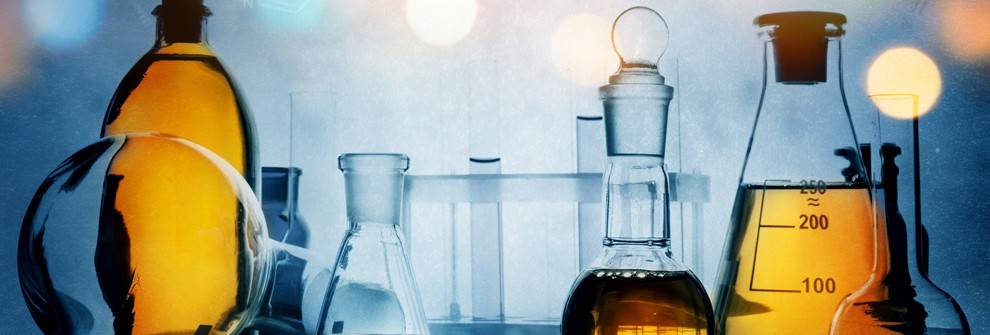
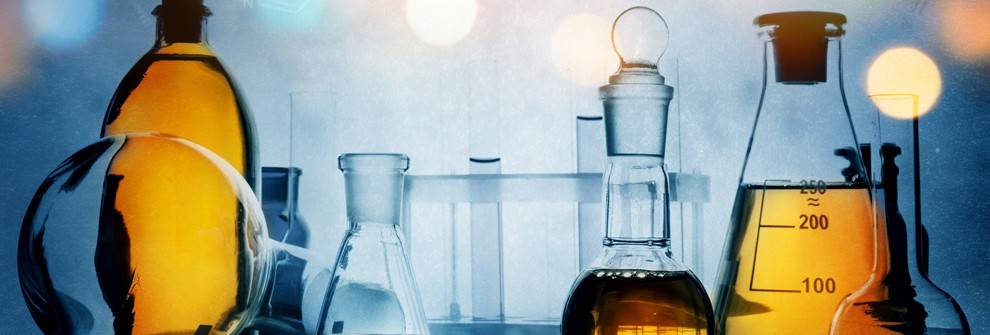
När man talar med ansvariga för underhåll av entreprenadmaskiner står det klart att blandade fordonsparker har blivit en norm. De flesta talar om interna besparingskrav och varierande kvalitet på utrustning från olika tillverkare som de huvudsakliga skälen till att de inte längre håller sig till enbart en tillverkare.
Blandade fordonsparker kan visserligen ge lägre kostnader och ibland även ökad prestanda, men det finns även nackdelar och den huvudsakliga är ett dramatiskt mycket mer komplicerat underhållsschema. Olika maskintillverkare har specificerar olika intervall för service och underhåll, olika krav och olika smörjmedelsbehov vilket gör underhållet till ett svårt jongleringsnummer.
Hur hanterar man det? Många underhållsansvariga har en konservativ inställning till underhållsscheman och oljebytesintervall och vill gärna hitta ett gemensamt bytesintervall som fungerar för hela fordonsparken. Detta resulterar dock alltför ofta i att service och oljebyten schemaläggs oftare än vad som behövs – och oftare än maskintillverkarnas rekommendationer. Det här konservativa underhållsschemat, resonerar man, kan ses som en billig ”försäkring” som de tror kan ersätta behovet av regelbunden oljeanalys.
Det man inte inser här är att oljeanalys inte enbart handlar om olja. En oljeanalys kan hjälpa er att identifiera många typer av problem med utrustningen – förekommer bränsleutspädning, föroreningar av smuts, kylvätskeläckage eller något annat problem som kan påverka utrustningens prestanda? Oljeanalys hjälper er också att förutse och ofta även undvika oväntade haverier.
Genom att bestämma ett gemensamt underhållsschema för hela fordonsparken, och avstå från oljeanalys, kan ni komma att öka kostnaderna för material och arbete och samtidigt öka risken för ett katastrofalt haveri på varje maskin med så mycket som 11 %.
Vi kan titta på kostnaderna för en vanlig typ av maskin, till exempel en väghyvel. Oljebyten, inklusive kostnaden för olja, filter, hantering av spillolja och arbete, kostar omkring 15 000 kr om året. Om vi antar att er fordonspark har 100 liknande maskiner som får en oljeservice fyra gånger om året, innebär det att ni spenderar 1 500 000 kr per år på oljebyten. Genom att regelbundet utföra oljeanalyser skulle ni i genomsnitt kunna eliminera minst ett oljebyte per maskin och år. Det innebär, med andra ord, att ni spenderar 375 000 kr mer än ni behöver på oljebyten varje år. Och då har vi inte räknat med den extra stilleståndstiden, som kan kosta betydligt mer än kostnaderna för själva oljebytet.
Utan regelbunden oljeanalys minskar också möjligheterna att kunna förutse vanliga typer av haverier. 40 % av alla motorhaverier beror till exempel i någon mån på föroreningar i kylsystemet, något som kan upptäckas vid en oljeanalys. Vad kostar det normalt att byta ut eller renovera en motor som fått skador av kylvätska? Låt oss anta ett medelvärde på ca 800 000 kr. Låt oss också försiktigtvis anta att vi råkar ut för en oförutsett motorrenovering om året. Addera den kostnaden till de 375 000 vi lade ut på ett extra oljebyte, så blir resultatet att den ”billiga försäkringen” kostar oss bortåt 1 200 000 kr om året.
Ett omfattande program för förebyggande underhåll där ni enkelt kan hålla reda på alla olika intervall som rekommenderas av maskintillverkarna och schemalägga ert underhåll efter dessa, och som inkluderar regelbunden oljeanalys, kan hjälpa er att minska er oljeförbrukning med i genomsnitt 25 % och dessutom resultera i bättre tillgänglighet och utnyttjande av utrustningen. På så vis kan ni serva rätt utrustning vid rätt tidpunkt och upptäcka möjliga risker för haveri innan de inträffar. Det här kommer inte enbart att leda till minskade materialkostnader, utan också till optimal produktivitet och maximal avkastning på investerat kapital för varje fordon.
Hur fungerar det serviceprogram ni använder idag jämfört med hur ni skulle vilja att det fungerade?